Packaging machinery manufacturers face a recurring challenge: the parts they need are often too complex, too unique, or too low in volume to justify traditional production methods. When equipment sits idle waiting on parts – or when changeovers demand rapid customization – time and cost pressures intensify.
Additive manufacturing is changing that reality. It’s not just a workaround; it’s now a preferred method for producing, modifying, and maintaining industrial machinery components.
This article breaks down the most common applications of 3D printing in packaging machinery – from grippers and ducts to feed screws and sealing components. You’ll see how manufacturers are replacing CNC, reducing lead times by over 90%, and cutting costs up to 98% across production and spare parts. We’ll also explain the role of different technologies (FDM, SAF, and P3), real-world case studies, and when each platform makes sense on the shop floor.
Why Traditional Methods Fall Short
Injection molding and CNC machining have long served industrial manufacturing. But in the context of packaging machinery – where product formats change frequently and equipment uptime is non-negotiable – they often fall short.
- Tooling costs can run into thousands of dollars per part, even for simple brackets or trays. For OEMs producing small batches or custom formats, the return on investment rarely adds up.
- Lead times for machined or molded parts often exceed 4–6 weeks. That’s unacceptable when a broken gripper or guide rail holds up a full production line.
- Design changes – even minor ones – require retooling or remachining, which delays implementation and increases scrap or obsolescence risk.
- Inventory buffers become a necessary evil. To avoid downtime, many plants stockpile custom parts, tying up capital and warehouse space for items that may never be used.
These challenges are magnified in packaging, where low-to-mid volumes, SKU variability, and machine-specific adaptations are the norm – not the exception. Parts like end-of-arm tools, vacuum ducts, sensor mounts, and soft grippers often differ by customer, container type, or changeover frequency.
To keep production moving and reduce risk, OEMs and operators are increasingly shifting to 3D printing (also known as Additive Manufacturing) as a primary method for producing these components. It allows teams to bypass traditional constraints entirely – delivering parts in days, not weeks, and adapting designs without incurring setup costs.
Where 3D Printing Excels
Additive manufacturing solves the challenges traditional processes can’t – especially when it comes to flexibility, speed, and part complexity.
- No tooling required: You can go straight from CAD to part, eliminating weeks of delay and thousands in upfront cost. Whether you’re replacing a broken duct or creating a custom tray for a new product SKU, production can start immediately.
- Cost reductions of up to 90%: Especially in low-volume applications, 3D printing dramatically lowers per-part cost by removing the need for molds, setups, or minimum order quantities. For example, SAF technology has produced functional conveyor links for just 3.10$ USD each, replacing components that previously cost over 130$ USD.
- Rapid prototyping and change-ready design: Engineers can test, refine, and implement new designs in hours. This is especially useful for end-of-arm tools, which often require fine adjustments to match product geometry or line layout.
- Lighter parts, better performance: Swapping machined metal components for engineered polymers like Nylon 12 Carbon Fiber reduces weight without sacrificing strength. In pick-and-place applications, this can directly increase machine speed and reduce energy use.
- No MOQs: Whether you need one feeder bracket or 15 soft grippers, you can print exactly what’s needed – when it’s needed. This makes spare parts and iterative testing practical without bloating inventory.
Common applications include trays, brackets, ducts, carriers, guides, and sealing parts. These can be printed, installed, and tested within 24 to 72 hours – enabling faster maintenance, faster product launches, and faster changeovers.
Technology Overview: Matching Tools to the Task
3D printing isn’t one-size-fits-all. The right platform depends on the part you need, the material requirements, and the production volume. In packaging machinery, three core technologies stand out – each with its own strengths.
FDM (Fused Deposition Modeling)
FDM is the most established form of industrial 3D printing. It works by extruding heated thermoplastic filament layer by layer. FDM is best suited to:
- Large, functional parts like housings, brackets, and trays
- Rugged applications where durability and strength are key
- Teams looking for a proven, cost-effective technology with broad material compatibility
FDM systems like the Stratasys Fortus 450mc and F900 can print in materials including ABS, ASA, PC, and carbon fiber-reinforced Nylon 12 – ideal for replacing CNC parts with a lighter, faster alternative.
SAF (Selective Absorption Fusion)
SAF uses a thermal inkjet process to fuse polymer powder into strong, detailed parts. It’s designed for:
- Low-to-mid volume production runs
- End-use parts that must hold up on the factory floor
- Complex geometries with no need for support structures
With build volumes up to 315 x 208 x 293 mm, SAF is perfect for printing ductwork, clips, feed screws, and conveyor components in PA11, PA12, or PP. It also offers consistent surface finish and tight tolerances, even across large batches.
P3 (Programmable Photopolymerization)
P3 technology is designed for precision. It uses light to cure resin materials layer by layer – similar to DLP, but with better control and part quality. P3 excels at:
- Soft-touch components like suction cups, gaskets, and flexible seals
- Biocompatible and sterilizable parts used in hygienic packaging environments
- Designs with fine details or complex internal features
Materials range from Shore 25A silicone to rigid resins with high impact strength. The Stratasys Origin can produce elastomeric parts that retain their performance after over 1,000 hours of use.
Whether you’re replacing a machined bracket, speeding up a changeover, or solving a sourcing issue, these technologies give packaging teams new flexibility – tailored to the demands of production, with a wide range of industrial-grade materials including carbon fiber, nylon, TPU, PP, PA11, and silicones.
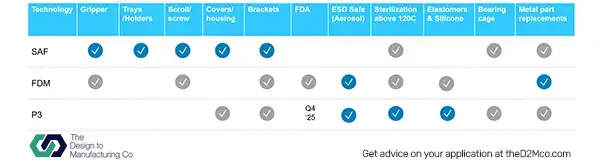
Real-World Use Cases in Packaging Machinery
Delkor’s Shift from CNC to SAF and FDM
Delkor Systems is a US-based OEM that builds advanced secondary packaging machinery for food, beverage, and consumer goods brands. Like many packaging machine builders, their success relies on speed, flexibility, and uptime across highly customized equipment.
Traditionally, Delkor machined every gripper and end-of-arm tool (EoAT) in metal. But with product formats constantly evolving, this approach became slow and expensive – especially when new tools were needed mid-project or in low volumes.
Today, Delkor 3D prints 75% of these parts using SAF and FDM technologies, keeping only 25% CNC machined. This shift allows their high-speed loaders to hit speeds of up to 200 containers per minute, thanks to lighter tools and faster design turnaround.
Manufacturers across Saudi Arabia, Qatar, and the UAE are under similar pressures – delivering tailored packaging formats for FMCG, pharma, and industrial products while maintaining throughput. The Delkor model shows that it’s not only possible to localize production of tooling and replacement parts – it’s faster, cheaper, and easier to adapt when additive manufacturing is in place.
Whether you’re an OEM building machines or a factory operator running them, Delkor’s success is a signal that additive isn’t just for prototypes – it’s a real production enabler.
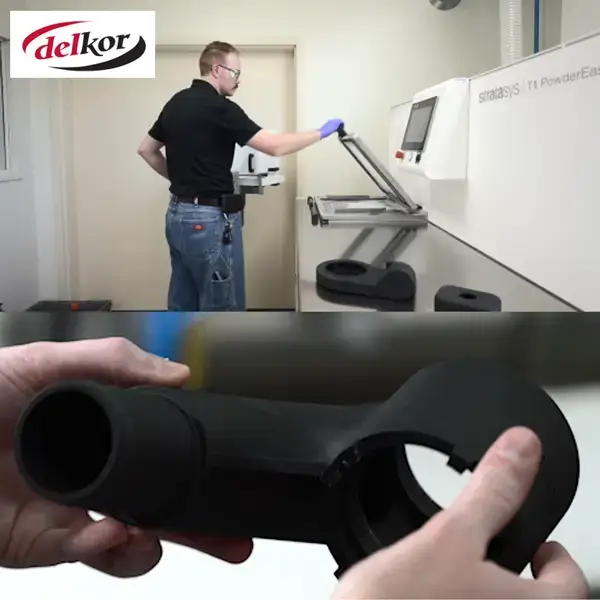
Vacuum Duct for EoAT: High Mix, Low Volume Made Easy
In many packaging lines, vacuum-based grippers are used to handle lightweight containers, cartons, or pouches. The ducts that guide air to these end-of-arm tools (EoATs) are often highly specific – shaped around product geometry, arm layout, and pressure requirements.
Traditionally, even small changes to a vacuum duct design required CNC machining, with lead times stretching into weeks. That’s a problem in fast-paced operations with frequent changeovers or short product runs.
With SAF printing and PowderEase post-processing, one manufacturer cut that lead time to just hours. The duct now prints in a single build, ready to use with minimal post-finishing. The switch delivered a 60% cost reduction, 30-minute savings per build cycle, and reduced component weight – improving pick-and-place speed and system responsiveness.
If you’re producing multiple formats (e.g. twin packs, travel sizes, or promotional variants), or supplying clients with constantly shifting requirements, this approach eliminates delays. You can reprint ducts in-house, adapt tools without re-machining, and avoid outsourcing each time product specs change.
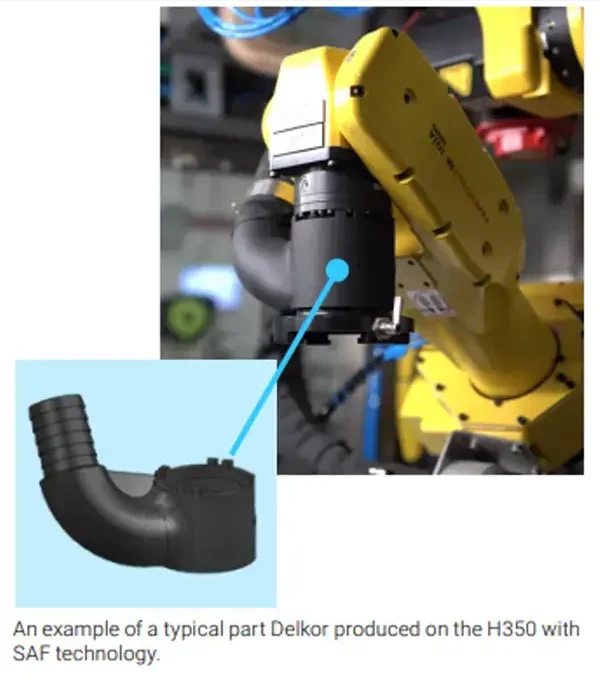
Flexible Parts: Gaskets, Seals, and Soft Grippers
Soft components are often the most difficult parts to source and the first to fail. In packaging, they perform critical roles – sealing air, absorbing shock, gripping delicate items, or complying with uneven surfaces. Their geometries are often non-standard, and their materials must strike the right balance between flexibility, durability, and hygiene.
Traditionally, these parts are molded from silicone or rubber, which means long lead times, high tooling costs, and limited options for customization. Changing a seal shape – even slightly – can delay a project by weeks.
This is where P3 technology and the Stratasys Origin platform stand out. By printing parts directly in flexible, production-grade materials, manufacturers gain the ability to:
- Create soft components with shore hardness from 25A to 90A
- Use biocompatible, sterilizable materials that pass ISO 10993 testing
- Achieve performance stability for 1,000+ hours of mechanical cycling
- Print designs that would be impossible to mold – like internal channels or compound curves
Typical packaging use cases include:
- Custom suction cups designed around non-standard product shapes
- Pneumatic grippers that require both flexibility and precision
- Gaskets and seals for hygienic lines handling food, beverage, or pharma SKUs
For manufacturers in the Gulf, where import dependencies and lead times often disrupt packaging schedules, in-house printing of soft parts reduces downtime and ensures you’re not waiting on international suppliers for elastomer tooling.
It also enables rapid validation of new designs – whether you’re building a new line or adapting an existing one – without locking into tooling decisions too early.
Conveyor Repairs Made Affordable
Conveyor systems are the backbone of many packaging lines – moving products between filling, sealing, inspection, and boxing stations. But when even a single link in the chain breaks, the entire line can grind to a halt. Worse, sourcing replacements for aging or proprietary belts is often slow, expensive, or flat-out impossible.
That was the case for US-based Goetsch’s Welding & Machine, who needed to replace 75 broken links in a legacy conveyor belt. The original belt assembly had been discontinued, and ordering a full replacement would have cost over 10,000$ USD, with weeks of downtime expected.
Instead, the team turned to SAF 3D printing. Using the H350, they reproduced the belt links at a material cost of just 3.10$ USD per part, each one printed with pinpoint precision to match the interlocking geometry of the original system. All 75 parts were delivered in days, not weeks – allowing the team to restore production with over 9,760$ USD saved.
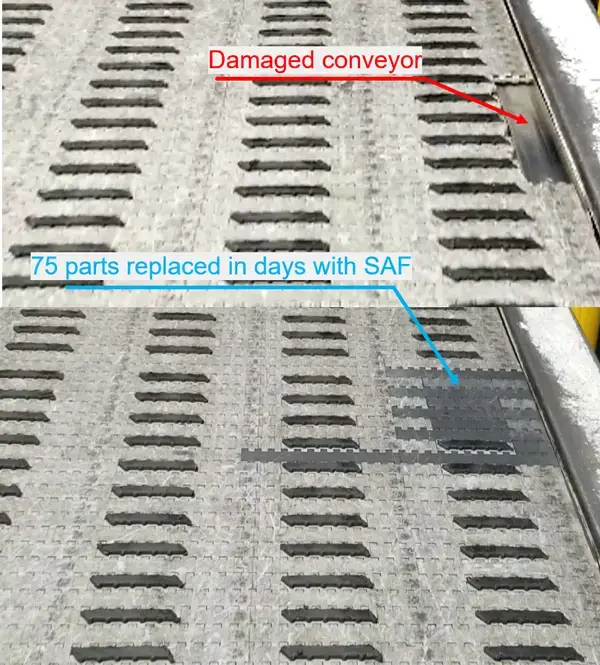
For manufacturers – especially those operating hybrid fleets of new and aging equipment – this case highlights a strategic opportunity: spare parts no longer need to be purchased, shipped, and stocked from overseas. You can recreate what you need in-house or with a regional partner, even if the OEM no longer supports the product.
It also changes how we think about obsolescence. If a part can be scanned, drawn, or measured – it can be replaced. With additive manufacturing, legacy equipment becomes maintainable again, extending asset life and reducing dependency on single suppliers.
Feedscrew Production in 12 Hours
Feedscrews (also called timing screws or bottle spacers) are used to precisely control the spacing and orientation of containers as they move along a conveyor – especially before capping, labeling, or inspection stations. Their design must match the shape and size of the product exactly, often with sculpted profiles that require custom CNC machining.
Traditionally, feedscrews are carved out of solid plastic or metal – a process that can cost 500$ USD or more per unit and take several days of setup and cutting. This makes them expensive to replace and difficult to justify for short product runs or frequent changeovers.
Using SAF printing on the Stratasys H350, one manufacturer produced 35 feedscrews in a single 12.5-hour build, at just 50$ USD per part – a 90% cost reduction with no compromise in quality. The prints achieved the necessary dimensional accuracy and were made in PA11, PA12, or PP depending on the application, all of which are suited for the demands of packaging environments.
Whether you’re bottling beverages in Dammam, filling cosmetics in Doha, or running short SKUs for retail in Dubai, printed feedscrews make it feasible to switch formats without incurring tooling delays or inventory bloat. You can test new bottle shapes, roll out seasonal variants, or replace worn screws in hours – not weeks.
Even better, the same design file can be reprinted anytime without additional cost. This turns format changeovers into a repeatable, scalable process – one that supports flexibility without driving up overhead.
Smart Redesign: TPU Gripper Replaces Spring
On high-speed packaging lines, grippers are responsible for picking, holding, or positioning products during movement and transfer. Traditionally, many of these grippers are built using spring-loaded mechanisms that allow movement and flexibility. But springs bring problems – especially when hygiene, speed, and reliability are critical.
One customer’s original metal-spring-based gripper began to fail under daily use. Over time, the spring would bend or lose tension, affecting grip consistency. Worse, small fragments from the metal spring risked falling into the packaging zone – a serious contamination hazard in food and pharma applications.
The engineering team rethought the design using TPU 92A, a flexible elastomer material printed on a Stratasys F370. By replacing the metal spring with a fully printed flexible element, they eliminated moving parts, simplified assembly, and increased the system’s mean time between failure (MTBF) by 20x.
Key benefits included:
- No risk of foreign object contamination
- Maintenance cycles extended significantly
- One-piece, print-ready design – no need for post-assembly or fastening
- Cost-effective enough to replace on demand, rather than repair
If your facility handles sensitive packaging – especially food, beverage, or medical items – removing sources of mechanical failure or contamination is critical. Replacing springs, seals, or hinges with printed elastomers can cut unplanned downtime, reduce QA rejections, and simplify preventive maintenance schedules.
And because TPU grippers can be printed in-house, you’re no longer waiting on imported parts or assembly – a major advantage in remote or fast-moving production environments.
Cable Energy Chain: No Assembly Required
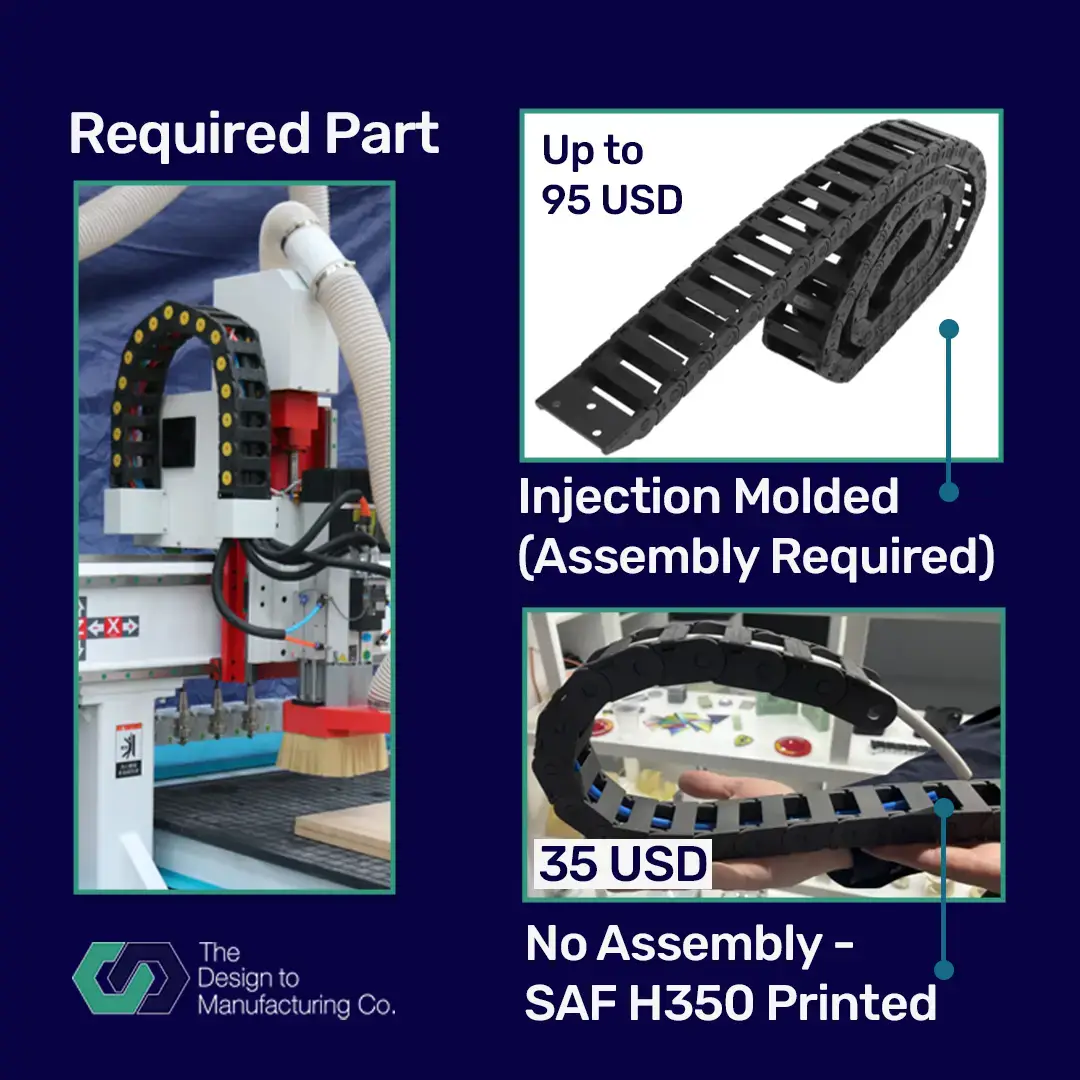
Most engineers don’t think twice about energy chains – until one breaks, or doesn’t quite fit. These critical components protect power and pneumatic lines in motion-heavy zones of the packaging line, yet they’re often treated as off-the-shelf parts.
But when space is tight, or motion paths are custom, standard chains fall short. The old solution? Manually assemble multiple injection-molded links into a chain long enough to do the job. It works – but it’s time-consuming, inventory-heavy, and rarely exact.
Now there’s a better way. With SAF printing, manufacturers can produce fully customized energy chains in a single, ready-to-install part – sized precisely to fit the machine’s geometry. No trimming. No rework. No spares bin full of leftover links.
In one case, a 1,000 mm cable chain was printed and delivered in under three days, with a 63% cost saving compared to the assembled version. More importantly, it removed a failure point and simplified the install.
For fast-moving facilities – especially in regional hubs where downtime is expensive and supplier lead times unpredictable – this type of quiet improvement adds up quickly.
Sustainability: SAF ReLife PA12 – Circular and Cost‑Effective
Sustainability is becoming a business requirement – not just a branding choice. For manufacturers in the Gulf and globally, cutting carbon emissions and material waste without compromising performance is now central to long-term strategy.
SAF ReLife PA12 addresses both objectives. Instead of relying solely on virgin polymer powder, this material uses reclaimed PA12 powder from other powder-bed printing processes. What was once classified as unusable waste is now converted into reliable, production-grade feedstock for SAF platforms.
The result? Significant environmental and economic benefits:
- Up to 89% reduction in CO₂ emissions when paired with renewable energy
- Approximately 43% reduction even under standard industrial energy conditions
- Around 20% cost savings per part compared to new PA12 material
ReLife PA12 still meets the performance requirements of functional components. It’s ideal for applications where strength, precision, and repeatability matter – but where lower carbon impact is also a priority.
For packaging manufacturers, it’s already being used for:
- Custom tray-forming tools
- Low-impact jigs
- Part guides and handling fixtures
- Non-load-bearing conveyor add-ons
This approach also reduces material procurement risks by extending the usable life of build powder. That means less waste, more control over cost, and measurable progress toward your internal sustainability targets—without sacrificing lead time or part quality.
Technology Fit: Typical Part Sizes
Not all 3D printing platforms are created equal when it comes to size. Choosing the right technology isn’t just about materials or speed – it’s also about ensuring the printer can reliably build the parts you need at the scale you operate.
Here are the maximum part sizes supported by each of the key technologies used in packaging machinery:
- SAF (Selective Absorption Fusion): Up to 315 × 208 × 293 mm
- FDM (Fused Deposition Modeling): Up to 914 × 914 × 610 mm
- P3 (Programmable PhotoPolymerization): Up to 192 × 108 × 370 mm
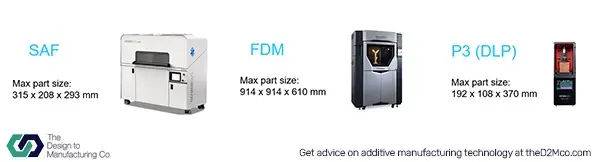
These dimensions define the outer limits of what a single part can be on each platform. But more important in day-to-day use is understanding the typical part size ranges where each technology performs best with minimal risk of warping, accuracy loss, or build failure.
Based on usage across production environments, the typical part size envelopes are:
- P3: 150 mm to 350 mm – best suited for small, detailed parts like seals, suction cups, or flexible grippers
- SAF: 300 mm to 600 mm – excellent for medium-sized ductwork, clips, fixtures, and conveyor tooling
- FDM: 200 mm to 1,000 mm – ideal for large brackets, structural supports, trays, and housings
Understanding these ranges helps prevent common pitfalls, such as overengineering a part that exceeds the printer’s stable build zone or choosing a platform unsuited to your target part geometry.
For packaging teams producing a mix of component types – like grippers, feed screws, guides, and trays – this insight is critical. It ensures you’re matching each job to the right platform, maintaining consistency, and avoiding wasted time or material.
When integrated into your production workflow, knowing these size profiles can also help standardize part categories across printers and simplify repeat ordering, digital inventory planning, and spare part scheduling.
Additive Opportunities by Component Type
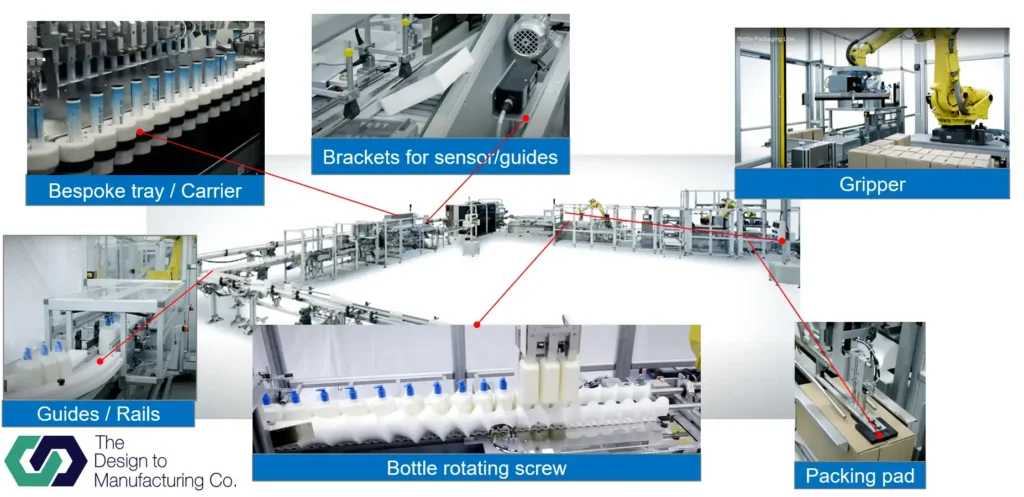
Additive manufacturing isn’t limited to prototypes or occasional fixtures – it now plays a daily role across full packaging environments, from OEM assembly to on-site maintenance. If you operate or support packaging machinery, chances are many of the parts you rely on are already viable candidates for on-demand printing.
Across packaging, lab, and automation environments, printable part types include:
- Sealing: gaskets, caps
- Brackets: mounts, housings
- Fluid handling: pipes, tubes
- Automation: trays, guides, end-of-arm tooling
- Electromechanical: connectors, wiring covers
- UI: knobs, handles, buttons
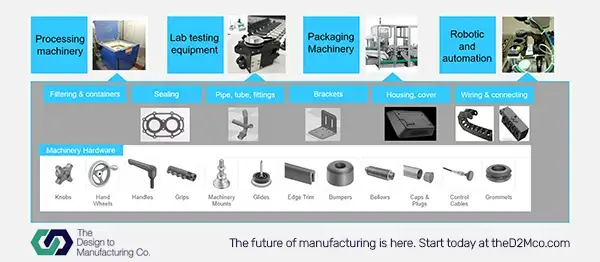
These parts can be produced without tooling and adjusted on demand – supporting leaner operations without long delays.
Each of these part types can be tailored for specific formats, product sizes, or hygiene requirements – then reprinted instantly as needed. For teams running high mix, high changeover operations, this creates a clear operational advantage.
Printed parts are not only cheaper but also more adaptable. They’re ready for real-time design changes, short production runs, or temporary installs – without waiting on tooling or committing to a full production order. It’s a smarter way to maintain uptime, reduce risk, and keep packaging lines responsive to market demand.
Why Stratasys for Industrial Component Manufacturing
In modern manufacturing environments, additive production is a part of the daily workflow. That’s why global OEMs and production teams rely on Stratasys systems to deliver the consistency, material performance, and reliability their operations demand.
Stratasys platforms are built for manufacturers who expect:
- Certified, production-grade materials, including ESD-safe, biocompatible, and FDA-compliant options
- Consistent part performance, even in demanding applications – like 25A silicone components proven to retain properties after over 1,000 hours of use
- Repeatable output across batches, enabling confident use of printed components on the line and in the field
- Scalable integration, from standalone units to fully networked, factory-ready systems
- Global support with local reach, offering service, training, and supply access in key regions – including growing adoption across the Gulf
Stratasys is the preferred additive partner for packaging machinery leaders not because it’s new – but because it works. Whether you’re sourcing components, replacing parts, or setting up in-house production capacity, the technology is proven, the infrastructure is in place, and the results are already measurable.
Stratasys systems are available in the Gulf region through the Design to Manufacturing Co. as certified Platinum Partners with deep industry knowledge. As a Platinum Partner, we’ve helped manufacturers across sectors evaluate, implement, and scale additive manufacturing with confidence. You don’t need to navigate the process alone – we provide region-specific guidance, real-world application support, and technology recommendations built on over 30 years of combined experience in design and production. Whether you’re just getting started or ready to expand, we’re here to support every step of your additive journey.
Ready to Bring Agility and Control Back to Your Production Line?
Additive manufacturing is no longer an emerging technology – it’s a practical tool for packaging manufacturers who need to move faster, reduce overhead, and stay in control of their parts and processes.
From end-of-arm tools and feedscrews to cable chains, seals, and brackets, production-ready 3D printing enables faster changeovers, lower costs, and local part availability – without compromising quality. And with materials certified for hygiene, safety, and performance, there’s no longer a trade-off between speed and standards.
Whether you’re replacing legacy parts, testing new formats, or planning a future-ready production line, the tools are already here – and so are the people who can help you put them to work.