Cable and wire manufacturers face growing pressure to deliver faster, cheaper, and more adaptable tooling. Traditional methods fall short when frequent design changes, custom insulation dies, or small-batch runs are required. This is where additive manufacturing – and specifically, Selective Absorption Fusion (SAF) technology – enters the conversation.
SAF-based printers like the H350 are transforming how parts for cable and wire production are made. By replacing CNC-machined aluminum tools with strong, heat-resistant thermoplastics, SAF users are cutting lead times, slashing costs, and accelerating development cycles – all without compromising quality.
SAF 3D printing for production parts
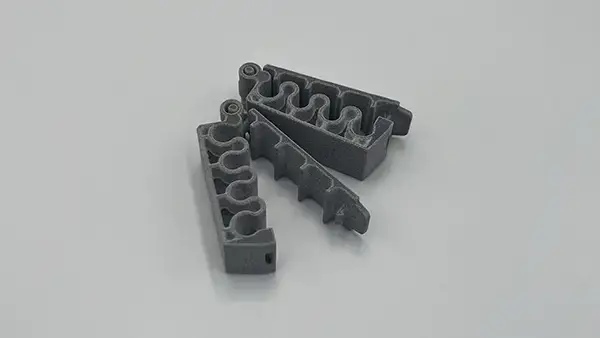
SAF is a powder bed fusion process that uses infrared-sensitive HAF (High Absorption Fluid) to selectively melt nylon-based powder, layer by layer. Unlike laser sintering, SAF uses a single-pass print carriage, which improves consistency and scalability. The result is high-strength, isotropic parts suitable for end-use in demanding industrial settings.
Cable manufacturers are using SAF to create:
- Wire guides and insulation tools
- Spooling and handling equipment
- Clamp blocks, fixtures, and tensioning components
- Replacement parts for older or bespoke equipment
These parts often require tight tolerances, heat resistance, and chemical durability. SAF delivers all three, with build speeds that rival or exceed traditional low-volume methods.
Replacing metal with SAF nylon
Many cable producers traditionally rely on aluminum for insulation guides, calibration tooling, and winding hardware. Machining these from metal takes days – and any design change requires a full remanufacture.
SAF allows manufacturers to print functional replacements in a matter of hours using PA11, a bio-based nylon with excellent mechanical strength and thermal resistance. For example:
- Die housings once milled from aluminum can now be printed overnight.
- Conductor guides are printed with tight enough tolerances to match machined equivalents.
- Tensioning and winding tools previously outsourced can be manufactured in-house.
One European cable factory replaced a full line of CNC-cut clamp blocks with SAF-printed versions, cutting tooling lead time by 80% and reducing spend by over 60%.
Reducing downtime with on-demand spare parts
Downtime in wire and cable production is expensive. If a winding block breaks or a guide wears out, waiting on external suppliers creates costly delays.
By setting up an internal SAF printing workflow, companies can store digital files instead of physical inventory. A replacement guide, once ordered externally with a 5–10 day lead time, can now be printed and installed same-day.
Even for rare or outdated components, 3D scanning and reverse engineering make SAF a practical option. Older parts from discontinued machinery can be digitized and reprinted – extending equipment life and reducing dependency on third-party suppliers.
Cable-specific benefits of the H350
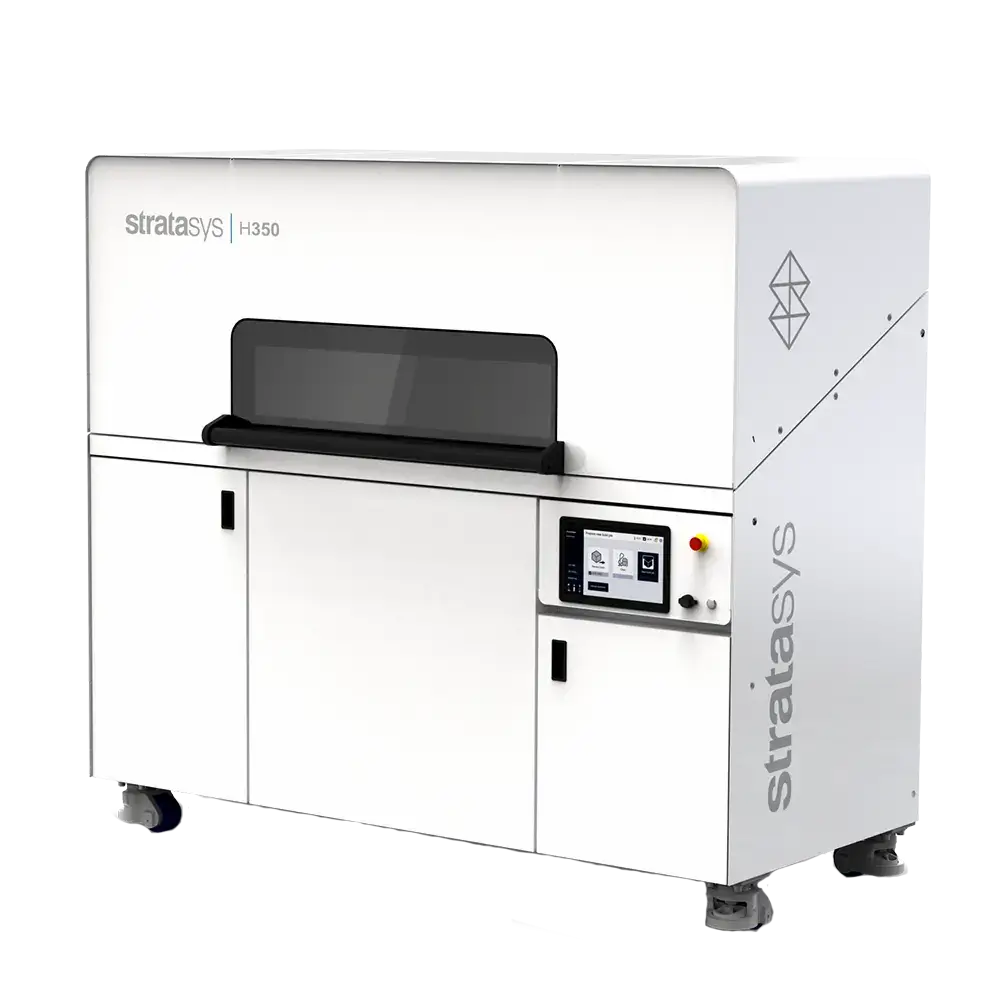
The Stratasys H350 printer – powered by SAF – is optimized for repeatable, large-volume part production. It features a 315 x 208 x 293 mm build volume and prints using PA11, a material well-suited to industrial environments.
Key H350 features for cable producers include:
- Consistent part quality across the full build tray
- Tight dimensional control suitable for high-tolerance fitment
- Minimal operator intervention for round-the-clock part production
- Powder reuse system to reduce waste and material cost
H350 users report up to 70% faster turnaround for cable-handling components versus traditional machining, particularly for high-mix, low-volume parts. Download the Stratasys H350 Product Brochure to learn more.
Driving development in cable insulation tooling
SAF isn’t just for spares – it’s accelerating product development too.
One manufacturer of specialty fiber-optic cables used SAF to prototype a new insulation nozzle in just 36 hours, compared to two weeks using metal tools. This rapid turnaround allowed them to test multiple versions in the extrusion line, refining flow and alignment before committing to final tooling.
Because SAF-printed parts closely replicate the performance of their metal equivalents, they can be used not only for testing but also for limited production runs. This is especially useful for:
- Pre-series cable designs
- Market-specific variants
- New product development
Using SAF to support leaner operations
Global supply chain disruptions have forced many manufacturers to rethink outsourcing. SAF offers an in-house alternative that aligns with lean manufacturing principles:
- Less reliance on external toolmakers
- Faster response to design changes
- Ability to print parts on demand, only when needed
This shift is especially relevant in Gulf-region markets like Saudi Arabia and the UAE, where local production capability is a strategic priority. Investing in SAF means greater autonomy and resilience for wire and cable businesses – with the added benefit of cost control.
Common SAF cable applications
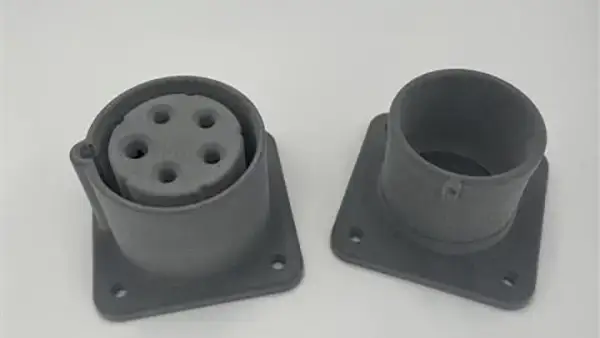
SAF’s precision and heat resistance make it ideal for:
- Conductor alignment tools – hold wires in position during extrusion
- Cable extrusion nozzles – guide insulation materials uniformly
- Winding and unwinding tools – support tension control during spooling
- Fixture blocks and mounts – hold cable in place for cutting or soldering
- Protective sleeves and baffles – prevent abrasion or damage in transit
Printed parts can be color-coded for identification, modified on the fly, and duplicated without tooling cost – ideal for high-mix production environments.
Getting started with SAF
Switching to SAF isn’t just about buying a printer and it’s material. It involves auditing current tooling workflows, selecting the right parts to convert, and setting up an efficient print-to-line process.
At The Design to Manufacturing Co., we help cable manufacturers plan their transition to additive manufacturing:
- Assess which components are suitable for SAF
- Set up secure digital inventories for on-demand use
- Provide support for equipment, materials, and file preparation
- Recommend the right H350 setup for your production volume
For companies producing complex cable assemblies, SAF printing is a cost-effective way to gain speed, flexibility, and control.
Explore how SAF 3D printing can improve your cable production speed and flexibility. [Request a quote] or [Book a consultation].