- August 29, 2023
- Posted by: TheD2MCo
- Category: News
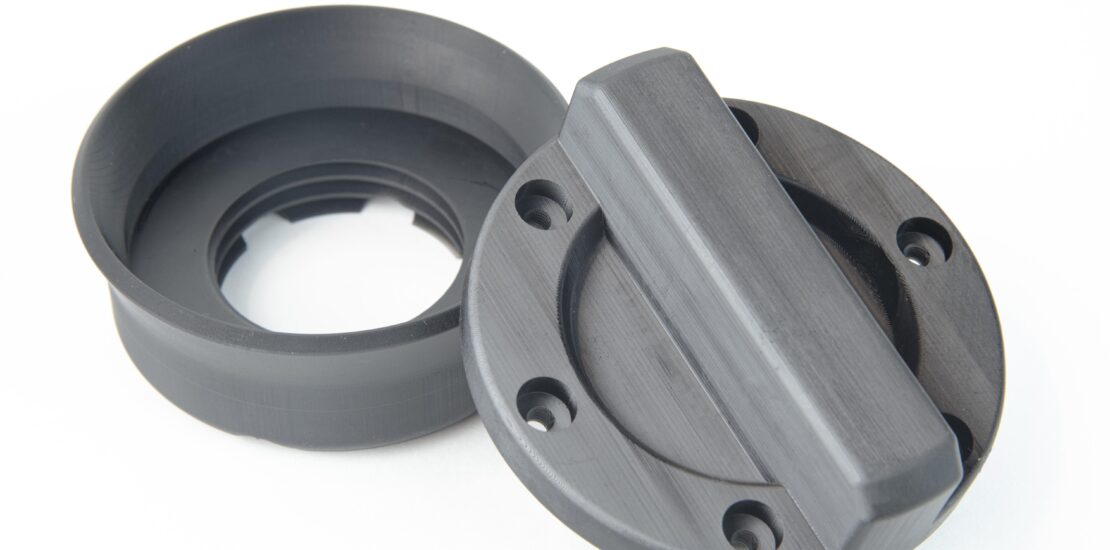
Often considered to be similar, DLP and LCD technology are actually very different technologies.
Often considered to be similar, DLP and LCD technology are actually very different technologies. Especially if you are looking to print high-performance materials and require accuracy and part quality: don’t let you get fooled into thinking they are interchangeable. Here’s a few reasons why.
As 3D printing makes its way to production, more technologies for printing production-grade parts emerge. Of these, DLP (Digital Light Processing) and LCD (Liquid Crystal Display, also called masked stereolithography or mSLA) are making most headway. Both use photopolymer resin in vat to create parts, layer by layer, by projecting light, and both offer fast printing times by projecting an entire layer at once. Players offering LCD technologies – Nexa3D, Photocentric and low-end printers like Anycubic and Phrozen, and the likes) compare their LCD technology to DLP, though that is comparing apples to oranges. The two technologies actually have several critical differences which are important to understand as they fundamentally delineate printer possibilities, i.e., materials and geometries that can be printed successfully. DLP vs. LCD – Let’s look at the differences and how they affect printer capabilities.
- Light Projection – DLP uses a digital projector to project light onto the resin, creating a highly accurate and detailed print. LCD uses an array of LEDs which are projected through a masking screen. These multiple UV light sources which inevitably vary slightly in intensity make it less uniform with some screens showing light bleeding between pixels, which results in less accurate curing of the layer. UV light also degrades the organic material of the liquid crystals quickly and uniformly, resulting in lower accuracy over time.
- Curing – The different method of projecting light causes parts to cure differently. With the LCD screen absorbing most of the energy (up to 90%), LCD technology often has lower irradiance – the amount of energy per unit area – than DLP (to avoid a too quick degradation of the LCD panels). Parts cured to a lower degree in the print will have inferior mechanical properties after post cure than those cured to a greater degree in the system. Parts remaining weaker may need more supports to add strength and stability during printing – especially when it comes to overhangs, bridges, islands and large cross-sections (bulky parts). Parts also must be taken off an LCD printer with more care to avoid damage.
- Resolution – At the core of the DLP light engine is the digital micromirror device (DMD) chip by Texas Instruments, which has a maximum 4K resolution. The bigger the projected area, the bigger the projected pixels (and the lower the XY resolution of the parts). LCD screens can be made in larger sizes, so LCD technology is better suited for printing larger objects.
- Tolerances – The DMD chip is manufactured with very tight tolerances, while the LCD panel is manufactured to be inexpensive (a necessity for a consumable). Tight tolerances result in better repeatability. DLP prints can be reliably reproduced with consistent results over time, making it a popular choice for end-use production. If requirements are not as rigorous, LCD is a cheaper alternative.
- Wavelength – LCD technology is limited to 405nm light engine wavelength as higher wavelengths degrade the LCD panel too quickly. DLP technology incorporates a 385nm light source. With the reactivity peak of most resins below 400nm, DLP can run a wider range of materials – especially high-performance resins. The different wavelength also influences resin curing, part quality, and mechanical properties: at 405nm, curing is less efficient even when the parts are given the same dosage of energy; the light penetrates deeper, dispersing the energy beyond the current printed layer. At 385nm, UV light is kept concentrated on each layer – printing more accurately –, while 405nm is much more susceptible to through-cure: curing that bleeds through the part geometry, curing too much resin and ruining the accuracy of intricate features. The efficiency of 405nm printing is greatly affected by tiny variations in the wavelength, while 385nm effectiveness is more stable.
- Purchase Price – LCD technology is typically cheaper than DLP technology. LCD printers have a simpler design and require fewer expensive components. The digital projector used in DLP printers is a high-end component that can add to the overall cost of the printer, as well as the optics needed to use 385nm UV light – which is absorbed by cheap optics. This makes an LCD printer more suitable for a limited budget.
- Total Cost of Ownership – As the UV light quickly degrades the LCD printer’s screen, it needs to be replaced often. This makes it a consumable item that can add to the overall cost of operating an LCD printer. The initial cost of a DLP printer is higher though costs less to operate. When comparing the cost of different technologies, make sure to calculate Total Cost of Ownership rather than only the purchase price of the printer.
DLP vs. LCD
In conclusion: LCD and DLP printers can both print certain parts and materials. Once you start taking a deeper dive into printing specific designs using highly specialized materials, for projects requiring repeatability, constant quality and high accuracy, LCD has problems to keep up.
Article written by Dorian Knight, PHD.